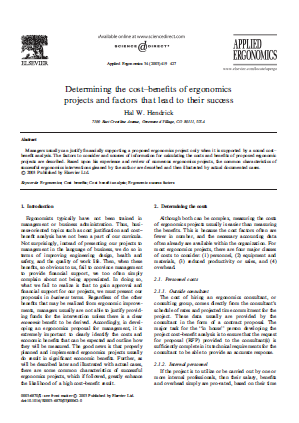
Regardless of the other benefits that may be realized from ergonomic improvements, managers usually are not able to justify providing funds for the intervention unless there is a clear economic benefit to be derived. Accordingly, in developing an ergonomics proposal for management, it is extremely important to clearly identify the costs and economic benefits that can be expected and outline how they will be measured.
Fortunately, properly planned and implemented ergonomics projects usually do result in significant economic benefits, and the literature consistently has shown that the earlier there is professional ergonomics participation in workplace design, the less costly is the effort.
For example, a number of studies have suggested the ergonomics portion of the engineering budget increases from about 1% of the budget when ergonomists are brought in at the beginning of a development project, to more than 12% when brought in after the system is put into operation.
This increase is believed to happen when ergonomists are brought in late in the project because serious human–system interface problems have surfaced that require major retrofits in order to correct them. A second major cost saving of early, or pre-emptive, ergonomics involvement can be in reducing the total cost of the design budget.
Personnel-related benefits from pre-emptive ergonomic involvement include:
Increased output per worker- Increased output per worker can be done for improvements in workplace design, hardware product design, software design and work system (macroergonomic) design.
Reduced error rate- Because correcting errors takes time, reduced errors frequently translate into increased productivity. Reducing errors also translates into fewer, accidents, and resultant reductions in equipment damage, personnel injuries, and related costs.
Reduced accidents, injuries, and illness- One of the most frequently encountered benefits. For example in one reported case study an ergonomically designed pistol grip type of knife was introduced to replace a conventional straight handle knife for deboning chickens and turkeys in a poultry packaging plant. This enabled the employees to de-bone the foul without having to significantly deviate their wrists, as was the case with the conventional knife. The resulting reduction in cases of carpal tunnel syndrome, tendonitis, and tenosynovitis translated into a saving in workmen’s compensation of $100,000 per year.
Reduced absenteeism- Reductions in lost time from persons failing to show up to work for reasons other than accidents, injuries, or illness, already noted, also is a common outcome of effective ergonomic interventions. Reduced absenteeism also can result in a productivity increase.
Reduced turnover- When ergonomic interventions improve the quality of work life, it is not uncommon to see a reduction in turnover rate, which can represent a significant financial benefit.
Reduced training time- Reductions in training requirements may come about because work system changes result in easier to perform functions and processes that require less time to learn. Alternatively, training requirements may be reduced because of:
(a) less turnover,
(b) reductions in lost time from accidents and injuries,
(c) less absenteeism, or
(d) because fewer people are required to perform a given function
Reduced skill requirements- Improved job designs and related work system processes may also result in reducing the skill requirements required to perform some jobs
Reduced maintenance time- Ergonomic improvements to jobs, worksites, equipment, or work systems can result in reducing the system’s maintenance requirements, thus requiring fewer maintenance personnel.